Abstract: ADX-600 is a core-shell acrylic impact modifier resin(AIM) manufactured through emulsion polymerization by our company. The product can serve as the impact modifier for PVC. ADX-600 AIM can replace CPE and MBS according to the comparison of various performance parameters between AIM and different PVC impact modifiers. The resultant PVC products demonstrate excellent mechanical properties, processing performance and a higher cost-effective performance.
Keyword: AIM, CPE, MBS, impact modifier, mechanical properties
Introduction
PVC serves as universal plastic with the largest yield and the wide application scope in the world. It has been widely utilized in aspects like building materials, industrial products, daily used pipes, sealing materials, fibers, etc. PVC demonstrates many excellent properties for a wide application in both industrial and civil sectors. However, PVC resin belongs to brittle materials. Its continuous glass phase cannot prevent the drastic expansion of cracks under stress and finally forms gaps and cracked rupture. Therefore, such kind of material displays a poor impact resistance. However, this shortcoming can be overcame by addition of impact modifier into PVC materials during their manufacturing and molding process.
Good impact modifiers should be featured by following excellent properties:
(1) A relatively low vitrification temperature Tg;
(2) The compatibility of impact modifier itself with PVC resin;
(3) Viscosity matching of impact modifiers with PVC;
(4) No obvious adverse effect on the apparent properties and the physical and mechanical properties of PVC;
(5) A good weather resistance and die swelling property.
The common impact modifiers for hard PVC mainly covers chlorinated polyethylene (CPE), acrylate (ACR), ethylene-vinyl acetate copolymer (EVA), methyl methacrylate-butadiene-styrene ternary graft copolymer(MBS) and acrylonitrile-butadiene-styrene copolymer (ABS). Among them, the chlorinated polyethylene impact modifier has been widely applied in China and acrylate is also being increasingly adopted because of its excellent properties. It has become a general concern how to improve the impact resistance and to facilitate the extrusion of plastic.
Our AIM product ADX-600 can replace CPE and MBS. It can significantly improve the fluidity and thermal deformation of PVC melt and thus facilitate PVC plastication. The resultant products demonstrate a high impact strength and a good weather resistance, stability and processing property with smooth, beautiful and highly glossy surface. Next, we have analyzed ACR, CPE and MBS in the following aspects.
I. Mechanism of Toughening by PVC Impact Modifiers
Chlorinated polyethylene (CPE) serves as linear molecules dispersed in PVC matrix in a network form. The principle of impact resistance is to form an elastic network in PVC matrix material so as to resist external impact. Such a network is prone to deform under tensile force. This will trigger the shear slip of the blend at an angle of 30°to 45° from the tensile direction, thus forming a shear band, absorbing a large amount of deformation energy, and enhancing the tenacity of blend system. The changes in stress yield of material under external force is shown in the following figures.
ACR and MBS belong to a kind of “core-shell” copolymer impact modifier. Its core serves as a low cross-linked elastomer, which plays main roles in tenacity enhancement and impact resistance. Its shell serves as a high-molecular polymer with a higher vitrification temperature, which plays main roles in protecting rubber core and improving the compatibility with PVC. This kind of modifier particles are easy to be separated and can be evenly dispersed into PVC matrix so as to form a “sea-island” structure. When the material is subject to external impact, rubber particles with low modulus are prone to deformation. At the same time, de-bonding and cavity are formed as the material is driven by PVC deformation with a high modulus. If those holes are formed close enough, the matrix layer between rubber particles can yield and enhance the tenacity of the material. The impact-resistant principle is shown in the figure below.
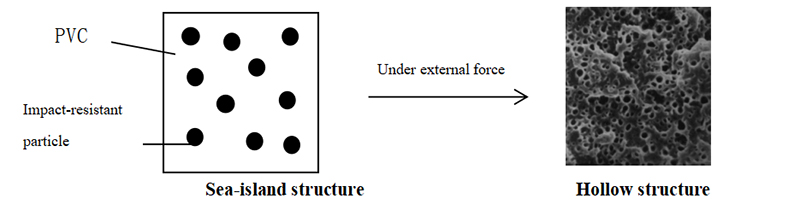
CPE, ACR and MBS demonstrate different sensitivity to machining strength due to their various toughening mechanism. During the processing, ACR and MBS particles are distributed in the PVC matrix through shearing action, forming an “sea-island” structure and thus enhancing tenacity of the material. Even if processing strength further increases, this structure won’t be compromised easily. The best toughening effect can only be fulfilled as CPE modifier and PVC are blended into a network structure that enfolds primary PVC particles. However, this network structure can be easily compromised due to changes in processing intensity. Therefore, it is sensitive to the processing intensity and applies to a narrow processing range.
II. Comparison of Various Properties between ADX-600 AIM and Different PVC Impact Modifiers
1. Base Material Testing Formula
Name | Organo-tin Heat Stabilizer (HTM2010) | Calcium Stearate | Titanium Dioxide | PE-6A | 312 | Calcium Carbonate | PVC-1000 |
Dosage/g | 2.0 | 0.7 | 4.0 | 0.6 | 0.2 | 5.0 | 100.0 |
2. Impact Property
Items | Sample Names | Testing Standards | Units | Additive Amount(phr) | |||||
3 | 4 | 5 | 6 | 7 | 8 | ||||
Impact From Notched Cantilever Beam | ADX-600 | ASTM D256 | KJ/m2 | 5.44 | 6.30 | 7.78 | 8.72 | 9.92 | 12.02 |
ACR From Foreign Countries | KJ/m2 | 4.62 | 5.01 | 7.68 | 8.51 | 9.63 | 11.85 | ||
MBS | KJ/m2 | 5.32 | 5.39 | 7.52 | 8.68 | 9.78 | 11.99 | ||
CPE | KJ/m2 | 3.54 | 4.25 | 5.39 | 6.32 | 7.01 | 8.52 | ||
Impact From Notch-free Cantilever Beam | ADX-600 | J/m | 57.03 | 63.87 | 72.79 | 88.23 | 100.09 | 121.32 | |
ACR From Foreign Countries | J/m | 46.31 | 50.65 | 72.55 | 85.87 | 97.92 | 119.25 | ||
MBS | J/m | 53.01 | 62.07 | 71.09 | 87.84 | 99.86 | 120.89 | ||
CPE | J/m | 21.08 | 37.21 | 47.59 | 59.24 | 70.32 | 82.21 |
3. Stretching / Bending Properties (All additive amount are 6phr)
Items | Testing Standards | Units | Technical Indicators (ADX-600) | Technical Indicators(ACR From Foreign Countries) | Technical Indicators(MBS) | Technical Indicators(CPE) |
Tensile Elasticity Modulus | ASTM D638 | MPa | 2546.38 | 2565.35 | 2500.31 | 2687.21 |
Tensile Elongation Yield | ASTM D638 | % | 28.38 | 27.98 | 26.84 | 17.69 |
Tensile Strength | ASTM D638 | MPa | 43.83 | 43.62 | 40.89 | 49.89 |
Bending Modulus | ASTM D790 | MPa | 2561.11 | 2509.30 | 2528.69 | 2678.29 |
Bending Strength | ASTM D790 | MPa | 67.39 | 65.03 | 66.20 | 69.27 |
Analysis: According to the above data on mechanical properties:
① Under the same doses, the performance of our product ADX-600 is better than that of MBS and ACR products from foreign countries. Our product can replace them in equal amount.
② Under the same doses, the performance of our product ADX-600 is much higher than that of CPE. Based on multiple tests, it has been verified that 3 doses of ADX-600 plus 3 doses of CPE can replace the usage of 9 doses of CPE. The specific mechanical properties are shown as follows.
Items | Testing Standards | Units | Technical Indicators(ADX-600/3phr+CPE/3phr) | Technical Indicators(CPE/9phr) |
Impact From Notched Cantilever Beam | ASTM D256 | KJ/m2 | 9.92 | 9.86 |
Impact From Notch-free Cantilever Beam | ASTM D256 | J/m | 97.32 | 96.98 |
Tensile Elasticity Modulus | ASTM D638 | MPa | 2250.96 | 2230.14 |
Tensile Elongation Yield | ASTM D638 | % | 101.25 | 100.24 |
Tensile Strength | ASTM D638 | MPa | 34.87 | 34.25 |
Bending Modulus | ASTM D790 | MPa | 2203.54 | 2200.01 |
Bending Strength | ASTM D790 | MPa | 60.96 | 60.05 |
4.Processing Actions
The diagram below shows the rheological curve. Red line: ADX-600/3phr+CPE/3phr; blue line: CPE/9phr
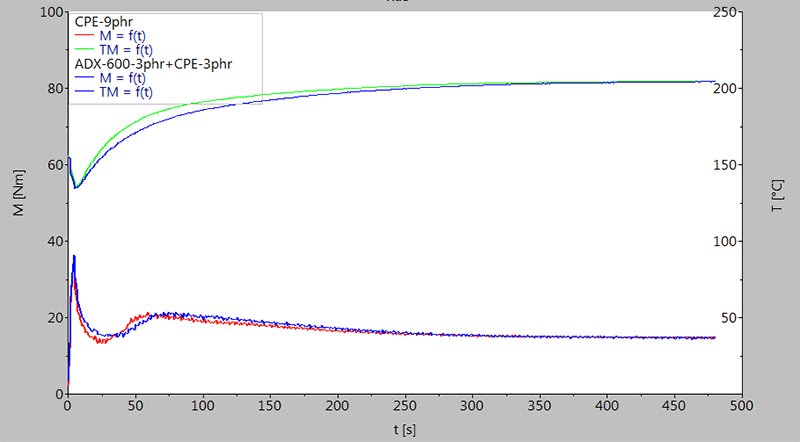
Balance torques of the two are basically the same, and the plastification of the material modified by ADX-600/3PHr +CPE/3PHR is slightly slower but within control according to the figure. Therefore, in terms of processing, 3 doses of ADX-600 plus 3 doses of CPE can replace the usage of 9 doses of CPE.
III. Conclusions
Through comparison between the ADX-600 AIM and the CPE and MBS in mechanical properties and processing behaviors, the following conclusion has been drawn upon objective analysis that 3 doses of ADX-600 plus 3 doses of CPE can replace the usage of 9 doses of CPE. ADX-600 AIM demonstrates better comprehensive performance, whose resultant products show better performance and higher cost-effective performance.
ADX-600 AIM belongs to an acrylate copolymer with core-shell structure. ACR demonstrates the better weather resistant, heat stability and performance-price ratio than MBS because the former contains no double bond. In addition, ACR also displays the advantages of wide processing range, fast extrusion speed, easy control, etc. It is mainly applied into hard and semi-hard PVC products, especially for chemical building materials and outdoor products, such as profiles, pipes, pipe fittings, boards, foaming materials, etc. It serves as a kind of impact modifier with large dosage at present and huge developing potential in the future.
Post time: Jun-20-2022